How AI is Revolutionizing Process Chemistry in Pharma and Chemical Manufacturing: A Focus on Scale-Up Operations
May 11, 2025 | by arms0013@gmail.com
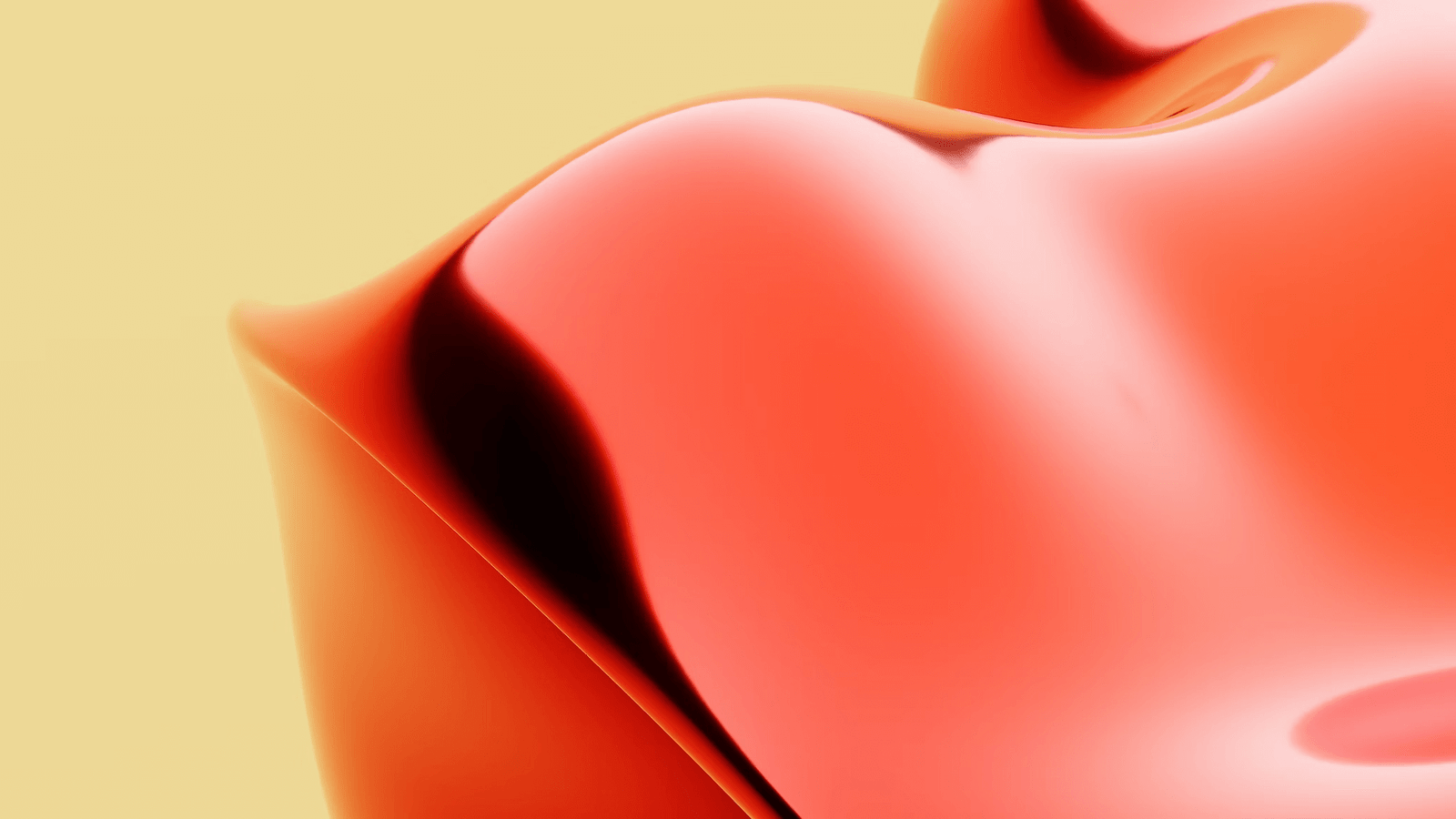
Introduction to AI in Process Chemistry
Artificial intelligence (AI) has emerged as a transformative force in various sectors, and process chemistry is no exception. In the realm of pharmaceutical and chemical manufacturing, the integration of AI technologies has become increasingly pivotal, especially during scale-up operations. The ability of AI to analyze vast datasets and derive actionable insights facilitates not only enhanced process efficiency but also risk mitigation in complex chemical environments.
Machine learning, a prominent subset of AI, has proven particularly beneficial in chemical process modeling. By applying algorithms to historical data, researchers can accurately predict outcomes such as yield prediction with AI, which ultimately optimizes production processes. Further, AI for reaction optimization enables scientists to identify ideal conditions for reactions by considering numerous variables simultaneously—something that would be arduous if done manually.
Equally essential is the role of AI in smart solvent selection. By utilizing machine learning techniques, chemists can efficiently sift through vast chemical libraries to identify the most suitable solvents for specific reactions. This streamlining not only accelerates the research and development phase but also enhances the sustainability of chemical processes. Moreover, AI-driven scale-up methodologies allow for more predictable transitions from laboratory settings to industrial metrics, a critical element in efficient pharma production.
Real-world applications underscore the value of these technologies. For example, several pharmaceutical companies have successfully implemented AI in chemical scale-up, leading to significant reductions in both time and costs associated with bringing new drugs to market. By harnessing the potential of AI in manufacturing, these companies enhance process safety while ensuring compliance with regulatory standards.
The increasing reliance on these advanced tools signifies a paradigm shift in how process chemistry is conducted, fostering innovation and efficiency in an evolving industry landscape.
Understanding Process Chemistry and Scale-Up Challenges
Process chemistry refers to the study and optimization of chemical processes involved in the production of pharmaceuticals and other chemical products. This discipline plays a critical role in transforming lab-scale synthesis into large-scale operations that are both efficient and economically viable. However, the transition from a controlled lab environment to a larger production scale brings with it a variety of challenges that can significantly impact product quality, production costs, and regulatory compliance.
One of the primary challenges in scaling up chemical processes is maintaining product quality. In laboratory settings, conditions such as temperature, pressure, and reaction time can be easily monitored and adjusted. Yet, when moving to larger vessels, these parameters can become less predictable. This variability can introduce inconsistencies in the final product, necessitating rigorous quality control measures. For instance, slight deviations in temperature during a reaction can affect the yield, leading to concerns around yield prediction with AI, which employs machine learning in chemistry to enhance accuracy in these predictions.
Another critical issue in scale-up operations is managing costs. The process must be designed to maximize output while minimizing waste and resource use. Innovative techniques such as smart solvent selection can lower costs and improve efficiency, yet the complexity of these processes can bring substantial risks. Moreover, compliance with regulatory standards in pharma production requires dedicated attention to safety and environmental impact, where process safety AI can be utilized to identify potential hazards and mitigate risks in real time.
Furthermore, the intricacies involved in chemical process modeling can complicate the implementation of scalable chemical synthesis. Each reaction may behave differently under varying conditions, thereby challenging the reproducibility of lab successes. As such, integrating AI for reaction optimization becomes essential, aiding in the development of robust methods that can withstand the rigors of industrial-scale operations. Understanding these challenges is vital for the successful incorporation of AI-driven scale-up strategies in process chemistry.
Benefits of AI in Scale-Up Operations
The integration of artificial intelligence (AI) in process chemistry, particularly in scale-up operations, yields significant advantages that enhance productivity and efficiency in pharmaceutical and chemical manufacturing. Traditional methods of scale-up often involve lengthy development cycles and unpredictability in product yield, presenting numerous challenges. By leveraging AI in chemical scale-up, organizations can streamline these processes, accelerating time-to-market and reducing costs.
One of the most notable benefits is the ability to conduct yield prediction with AI. Advanced algorithms analyze historical data to forecast yields based on varying inputs and conditions, enabling chemists to optimize formulations more effectively. This not only minimizes wasted resources but also leads to a more efficient and predictable scaling of chemical processes.
Another critical aspect is smart solvent selection. AI technologies analyze vast datasets to recommend the most appropriate solvents for specific reactions. This data-driven approach not only enhances the reaction’s efficiency but also increases safety by identifying solvents that minimize risks associated with hazardous materials. Additionally, AI for reaction optimization helps in fine-tuning conditions to achieve better outcomes during manufacturing.
The implementation of machine learning in chemistry also plays a pivotal role in enhancing process safety. AI-driven scale-up ensures that potential hazards are identified and mitigated early in the development process, protecting workers and the environment. By establishing a robust chemical process modeling framework, firms are positioned to predict and mitigate risks with unparalleled accuracy.
Furthermore, adopting ai in manufacturing promotes a more adaptive and scalable chemical synthesis methodology. This adaptability enables organizations to respond swiftly to market demands without compromising quality. Overall, the convergence of AI technologies in scale-up operations not only revolutionizes the approach to chemical production but also lays the groundwork for future innovations in the pharmaceutical sector.
Yield Prediction Models Enabled by AI
The integration of artificial intelligence (AI) and machine learning in chemistry has introduced transformative yield prediction models that are critical in the scale-up of chemical processes. Yield prediction with AI not only enhances the accuracy of forecasts but also streamlines resources during pharmaceutical production and chemical manufacturing. Traditional yield prediction methods often rely on empirical data and heuristics, which may not efficiently adapt to the complexities inherent in chemical reactions. In contrast, AI-driven approaches utilize large datasets to identify nuanced patterns and insights that might be overlooked in traditional methodologies.
One common technique involves the application of regression algorithms, which can effectively predict yields based on a variety of input parameters, including reaction conditions and catalyst types. For example, a study demonstrated that by employing machine learning in chemistry, researchers were able to increase yields by 20% when optimizing reaction conditions for a particular synthesis pathway. Additionally, advanced models such as neural networks and decision trees have been increasingly adopted for their ability to handle non-linear relationships and complex data structures, enhancing yield predictions.
Moreover, AI technologies facilitate smart solvent selection, optimizing solvent systems to improve yields and reduce waste. Case studies have showcased scenarios where AI recommended alternative solvents, leading to enhanced reaction efficacy and minimized environmental impact. Furthermore, the combination of chemical process modeling with machine learning techniques empowers scientists to not only predict yields but also to optimize reaction parameters proactively, ensuring scalable chemical synthesis.
In the realm of process safety, AI applications allow for enhanced monitoring of reactions, thereby minimizing risks during scale-up operations. The implementation of predictive analytics in drug formulation and production has proven instrumental in improving yield outcomes. These innovations position AI as a cornerstone of modern chemical scale-up operations, paving the way for more efficient, reliable, and high-yielding processes.
Solvent Selection: AI’s Transformative Role
The selection of solvents plays a pivotal role in the success of chemical reactions, especially during scale-up operations in pharmaceutical and chemical manufacturing. Traditional methods of solvent selection, often based on empirical knowledge and trial-and-error approaches, can be both time-consuming and inefficient. The integration of AI in process chemistry has significantly transformed the solvent selection process, leading to enhanced outcomes in yield prediction and improved overall efficiency.
AI-driven tools utilize advanced algorithms to analyze historical data and evaluate various experimental conditions, allowing for the identification of optimal solvents tailored for specific reactions. Machine learning in chemistry facilitates the examination of numerous solvent properties, such as polarity, boiling points, and environmental impact. By synthesizing this data, AI ensures that the selected solvents are not only effective but also compliant with current environmental regulations, thereby addressing the growing concerns around sustainability in chemical processes.
Moreover, AI in chemical scale-up further optimizes the solvent selection process by facilitating smart solvent selection. This involves predicting the behavior of solvents under different conditions and suggesting alternatives that may yield better results. Such autonomous capabilities not only reduce the time required for experimental validation but also enhance the predictability of outcomes, which is crucial in the pharma production sector where efficiency and compliance are paramount.
Additionally, AI for reaction optimization infuses a new level of precision into the solvent selection process. By leveraging chemical process modeling techniques, AI can simulate various scenarios to test potential solvent interactions, thereby maximizing reaction yields and minimizing by-products. As a result, AI-driven scale-up methodologies can lead to more scalable chemical synthesis approaches while ensuring that process safety is maintained. In sum, the application of AI in solvent selection is a game changer in the pursuit of efficient, safe, and compliant manufacturing practices in the pharmaceutical and chemical industries.
Risk Mitigation Through AI Insights
The landscape of chemical manufacturing and pharmaceutical production has undergone significant transformation with the integration of artificial intelligence (AI). One of the paramount contributions of AI in process chemistry is its ability to identify and mitigate risks associated with scaling up chemical processes. The complexity involved in scaling reactions from lab-scale to production-scale warrants innovative and reliable solutions to ensure product safety and quality.
AI enhances risk assessment by employing predictive models that utilize extensive historical data, coupled with real-time monitoring mechanisms. These models analyze various parameters, including reaction conditions, material properties, and environmental factors, to foresee potential operational issues. By recognizing patterns in historical outcomes, AI can help predict issues such as equipment failure or adverse chemical reactions, which are critical factors in the transition from small-scale experiments to larger manufacturing operations.
Moreover, the implementation of AI-driven insights fosters proactive decision-making, allowing for the early identification of fluctuations that may compromise process safety or yield predictions. By applying machine learning in chemistry, manufacturers can enhance their chemical process modeling techniques to ensure a smoother scale-up, thus reducing the likelihood of costly disruptions during production.
In addition to prediction and analysis, AI enables smart solvent selection and reaction optimization, which are vital in mitigating risks associated with chemical synthesis. The use of data-driven approaches in selecting solvents not only improves efficiency but also minimizes hazardous waste, aligning with modern sustainability objectives. Consequently, the deployment of AI solutions leads to scalable chemical synthesis that is both safer and more economically viable.
Ultimately, leveraging AI for risk mitigation in scaled operations not only safeguards the production process but also reinforces the commitment to operational excellence and safety in pharmaceutical and chemical manufacturing. These advanced methods represent a pivotal shift in how risk is managed, ensuring a resilient framework for future innovations.
Examples of AI Success in Pharmaceutical Scale-Up
The integration of AI in pharmaceutical scale-up operations has led to substantial advancements, transforming traditional methodologies into more efficient processes. One prominent example is a major pharmaceutical company’s use of AI for yield prediction. By leveraging machine learning algorithms, they were able to analyze historical data from previous batch productions, which improved their predictive accuracy for future yields. This predictive capability facilitated informed decision-making, ensuring that the scale-up process aligned with production goals while minimizing waste due to over or underproduction.
In another noteworthy case, a biopharmaceutical firm implemented AI-driven scale-up solutions for optimizing bioreactor conditions. Machine learning models were employed to analyze multiple variables—such as temperature, pH, and nutrient concentration—enabling the company to fine-tune these parameters for enhanced productivity. The result was a 30% increase in the yield of critical protein therapeutics, demonstrating the substantial impact of AI in reaction optimization and chemical process modeling.
Additionally, the smart solvent selection capability of AI algorithms facilitated a major chemical company in streamlining their solvent usage during scale-up. By employing data-driven insights to identify the most efficient solvents for chemical reactions, they reduced costs and improved safety protocols during the manufacturing process. The machine learning in chemistry approach has fostered greater compliance with process safety standards while enhancing the overall sustainability of the operations.
Lastly, a recent pilot program showcased the benefits of AI in identifying process bottlenecks in manufacturing lines. The AI tools analyzed real-time data flow to predict potential failures or delays, allowing for proactive adjustments prior to actual production issues. This capability paved the way for improved production reliability and operational efficiency across the board.
These examples underscore the critical role of AI in chemical scale-up processes, highlighting its ability to drive significant advancements in efficiency, predictability, and cost-effectiveness within the pharmaceutical industry.
Future Outlook for AI in Process Chemistry
The future of artificial intelligence (AI) in process chemistry and scale-up operations appears promising, driven by rapid advancements in machine learning algorithms, data analytics, and computational modeling. As industries strive to improve efficiency and reduce costs, integrating AI in chemical process modeling becomes increasingly crucial. The potential for yield prediction with AI tools can significantly streamline production methodologies, enabling manufacturers to forecast product output with greater accuracy. This predictive capability will allow companies to optimize their resources, ensuring they maintain high-quality standards while minimizing wastage.
One of the most exciting trends is the rise of smart solvent selection enabled by AI. The ability to analyze vast datasets and predict the most effective solvents for chemical processes can lead to enhanced scalability in chemical synthesis. Ultimately, this results in a more sustainable approach, as optimized processes consume less energy and materials. Additionally, the application of AI for reaction optimization can facilitate the discovery of innovative reaction pathways, thus accelerating the development of novel pharmaceuticals.
As AI technologies evolve, the potential for AI-driven scale-up solutions will reshape the pharma production landscape. Continuous improvements in process safety AI systems can help manufacturers identify and mitigate risks throughout the production cycle. With an increased focus on compliance with industry regulations, AI applications can play a crucial role in enhancing safety protocols while ensuring efficient operations. Furthermore, the incorporation of AI in manufacturing processes will contribute to the creation of more agile production environments that can swiftly adapt to changing market demands.
Furthermore, as AI capabilities advance, they will likely redefine industry standards, paving the way for more resilient and responsive supply chains in chemical manufacturing. Consequently, the future outlook for AI in process chemistry holds tremendous potential, setting the stage for a transformative impact on how chemicals and pharmaceuticals are developed and produced.
Ethical Considerations in AI and Chemical Manufacturing
The integration of AI in process chemistry, particularly in areas such as chemical manufacturing, has raised various ethical considerations that warrant careful examination. As industries increasingly adopt AI technologies for functions like yield prediction with AI and smart solvent selection, issues surrounding data privacy become paramount. The vast amounts of data collected for AI-driven scale-up processes can potentially include sensitive information, necessitating robust data protection measures to safeguard against unauthorized access and misuse.
Another significant ethical concern is the accountability of AI-driven decisions in chemical processes. These decisions affect not only production efficiency and cost-reduction but also process safety AI interventions that determine the safety of manufacturing practices. Establishing clear lines of accountability regarding AI outputs and their implications is essential to ensure that organizations remain responsible for the outcomes generated by machine learning in chemistry applications. The autonomy of AI systems must be balanced with human oversight to mitigate risks and enhance decision-making integrity.
Furthermore, the rise of AI in manufacturing may lead to potential job displacement within the workforce. Automation and AI-driven solutions can optimize processes and reduce the need for human intervention in specific tasks, which could lead to decreased employment opportunities, particularly for workers in lower-skilled positions. It is crucial for the industry to proactively address these challenges by investing in workforce retraining and upskilling initiatives that equip employees with the necessary skills to thrive in an AI-enhanced work environment.
Striking a balance between leveraging the advancements of AI for scalable chemical synthesis and addressing these ethical concerns is imperative for responsible development. Engaging in transparent discussions and establishing ethical guidelines can ensure that the adoption of AI in chemical manufacturing serves both technological advancement and societal good.
Conclusion
The integration of artificial intelligence (AI) in process chemistry and scale-up operations has notably transformed the pharmaceutical and chemical manufacturing landscape. Through techniques such as machine learning in chemistry, AI has enhanced yield prediction, facilitated smart solvent selection, and refined reaction optimization. This transformation allows for more efficient chemical process modeling and scalable chemical synthesis, leading to improved productivity and reduced time-to-market for pharmaceutical products.
AI-driven scale-up strategies have optimized the entire manufacturing process, from initial research and development to final production. By leveraging data-driven insights, manufacturers can now proactively address potential challenges associated with chemical scale-up, enabling them to achieve greater consistency and reliability in their operations. Furthermore, the use of AI for process safety not only mitigates risks but also ensures compliance with regulatory requirements, ultimately safeguarding both personnel and the environment.
It is vital, however, to remain cognizant of the ethical implications and the necessity for responsible AI deployment in these industries. The data utilized in AI applications can introduce biases or misinterpretations if not handled with care, highlighting the importance of robust data governance and transparency. Moreover, as AI in manufacturing continues to advance, stakeholders must prioritize collaboration between technologists and chemical engineers to harness AI’s full potential while mitigating the associated risks.
Looking ahead, the evolution of AI in process chemistry promises endless possibilities for innovation. By continuously adapting and evolving methodologies, the sectors of pharma production and chemical manufacturing stand to gain from further advancements in AI technologies, ensuring they remain at the forefront of the industry. This ongoing fusion of AI with traditional practices may one day redefine process chemistry as we know it.